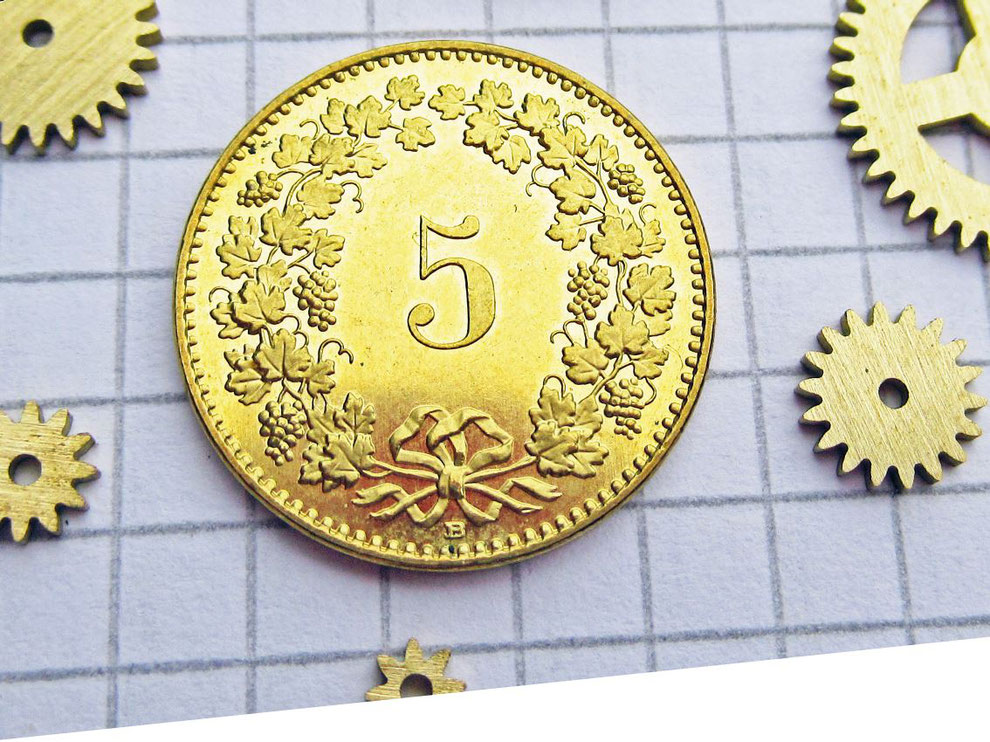
Das Mikro-Wasserstrahlschneiden wurde von Waterjet 2003 mitten in einer Krise entwickelt. Dies erforderte die Neukonstruktion komplett neuer Maschinen, Strahlkopf-Designs und Steuerungssysteme. Dadurch gelang es, eine zehnfach höhere Präzision als mit den damals am Markt erhältlichen Wasserstrahlanlagen zu erreichen. Mit dieser Technologie konnten Hightech-Branchen wie die Uhrenindustrie, die Feinmechanik und die Medizintechnik für den Einsatz des Verfahrens gewonnen werden. Ungeachtet der damit erzielten Erfolge hat sich Waterjet nicht auf diesen Lorbeeren ausgeruht. Die damals gegründete eigene Forschungsabteilung entwickelte seither die Grundlagen für immer weitere Innovationen und zusätzliche Einsatzgebiete.
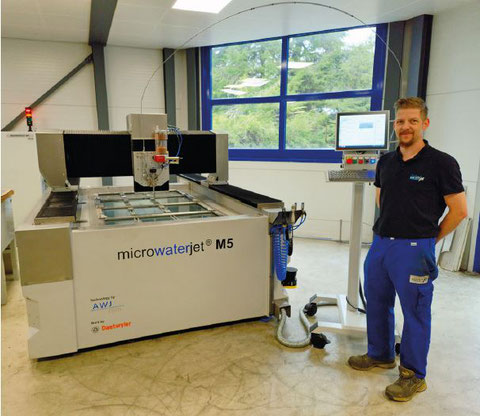
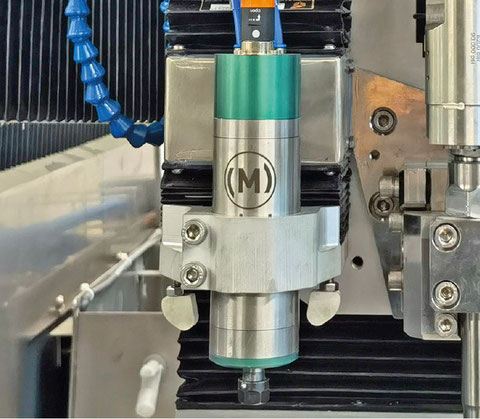
Sonderzubehör wie Hochfrequenzspindel bzw. Drehachse
«Optional sind bei unseren Anlagen mittlerweile Zusatzausstattungen wie eine Hochfrequenzspindel oder eine separate Drehachse verfügbar», ergänzt W. Maurer.
Die Ansteuerung dieser Geräte ist jeweils in die Maschinensteuerung integriert. Die fest an den Strahlkopf gekoppelte Hochfrequenzspindel verfügt über ihre eigene ZAchse und erreicht bis zu 50.000UPM.
Mit dieser Spindel sind ergänzend zum Wasserstrahlschnitt umfassende 3DFräsbearbeitungen möglich, beispielsweise das Vorab-Einbringen von Startlochbohrungen in heikle Materialien, das Ansenken von Durchgängen und das Anfasen von Vertiefungen oder Kanten, das Fräsen von Taschen sowie darüber hinaus alle möglichen weiteren Zusatzarbeitsgänge.
Dies erfolgt in der gleichen Aufspannung wie das Wasserstrahlschneiden, so dass sich der Anwender keine Gedanken über Positions-, Fluchtungs- oder Winkelabweichungen machen muss.
Üblicherweise wird die mechanische Bearbeitung vorab durchgeführt, gefolgt von der Beseitigung der Späne und der abschließenden Wasserstrahl-Schneidbearbeitung.
Mit der Drehachse können diverse Rohr- und Stabbearbeitungen bis hin zu Rohrdurchdringungen durchgeführt werden. Hierbei kann fallweise auch die Frässpindel zum Einsatz gebracht werden, um beispielsweise Fasen anzubringen.
Anschlussfasen in Richtung der Rohr-Hauptachse lassen sich bei schwer bearbeitbaren Werkstoffen auch ohne Einsatz der Frässpindel durch genau dosierte Wasserstrahlbearbeitung bei gleichzeitigem Einsatz der Dreh- und der in Richtung der Rohrachse verlaufenden Hauptachse erzeugen.
Möglich sind auch Bohrbearbeitungen, die nicht mit dem Durchmesser fluchten, sondern seitlich parallel dazu angesetzt werden. Mithilfe spezieller Tricks lassen sich auch Rohre aus spröden Materialien wie Glas, Keramiken oder Faserwerkstoffen wie GFK oder CFK durchtrennen, ohne dass es zu Beschädigungen durch plötzlichen Bruch im Bereich des Reststegs kommt.
Fortschritt und Innovationen
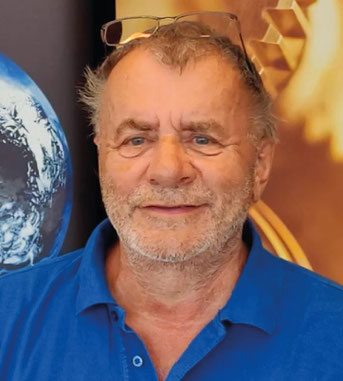
«Auch in den letzten Jahren konnten wir beim Mikro-Wasserstrahlschneiden weitere Durchbrüche erzielen», sagt Walter Maurer, Inhaber und Verwaltungsratspräsident der Waterjet AG in Aarwangen (Schweiz).
So sei es nach intensiver Entwicklungsarbeit gelungen, den Durchmesser des Wasserstrahls von 170μm noch weiter auf nur noch 150μm zu verringern. Das klinge zunächst nicht nach viel, doch ergäben sich für die Praxis dennoch weitreichende Vorteile.
Zunächst lassen sich dadurch je nach Einsatzfall engere Schneidspalte von nur noch 170μm erreichen. Noch wichtiger sei jedoch, dass durch diese Verbesserung jetzt viele weitere Teile unter Einhaltung der geforderten Toleranzen bearbeitet werden können, bei denen dies bisher nicht darstellbar war.
Am Werkstück sind heute je nach Materialdicke Genauigkeiten von bis zu 5μm erzielbar. Zusätzlicher Plusfaktor sei die Verwendung einer Höchstdruckpumpe mit 6.200 bar, mit der größere Arbeitsfortschritte und/oder die Bearbeitung dickerer Materialien möglich seien, insbesondere auch beim Einsatz von Reinwasser zur Bearbeitung biokompatibler Werkstoffe.
Weitere Besonderheit sei die Weiterentwicklung der Steuerung. Diese beinhalte jetzt eine verfeinerte Kontrolle der Arbeitsparameter gerade auch bei heiklen Geometrien wie scharfkantigen Ecken.
Das ermöglicht eine Optimierung der Bearbeitungszeiten bei zugleich verbesserter Präzision gerade in diesen Bereichen. Auch verfügt die Steuerung jetzt über eine erweiterte Materialdatenbank mit vordefinierten Parametersätzen für die Bearbeitung einer großen Bandbreite industriell eingesetzter Werkstoffe.
Ein weiteres Forschungsfeld betreffe die Diversifizierung im Bereich der Abrasivmaterialien. Hier würden spezielle Kornspektren des «klassischen » Granatmaterials ebenso untersucht wie alternative Mineralien oder Speziallegierungen.
Superfeines Abrasiv für bessere Mikro-Schnittkanten
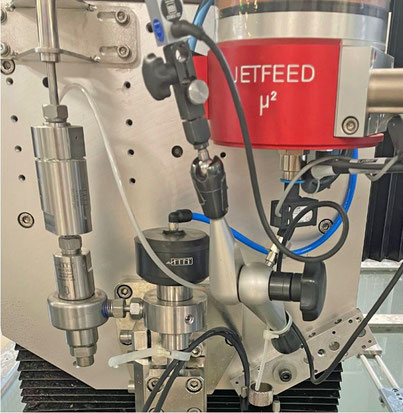
Einen weiteren wesentlichen Fortschritt erzielten wir dank der Entwicklung einer neuen Strahlkopftechnologie für superfeines Abrasivpulver», freut sich W. Maurer.
Entscheidend sei dabei nicht nur die Entwicklung spezieller Aufbereitungsverfahren, sondern auch der Übergang zur Verwendung einer pastösen Masse statt der «klassischen» Verwendung von rieselfähigen Pulvern.
Je feiner der Durchmesser der Körner, desto größer werden leider die Schwierigkeiten beim Fördern und Dosieren.
Die für diese Anwendung speziell aufbereiteten Pasten werden beim Eintritt in die Mischkammer vom feinen Wasserstrahl mit einem Durchmesser von nur noch 150µm in kleinsten und genau reproduzierbaren Mengen mitgenommen.
Das Ergebnis ist nicht nuräußerst präziser Schnitt; ebenso wesentlich ist auch die Tatsache, dass die Schnittkanten eine außergewöhnlich hohe Oberflächenqualität aufweisen. Das ist für viele Anwendungen – beispielsweise bei den Flanken von Zahnrädern für die Feinmechanik – ein erheblicher Pluspunkt.
ISO 13485-Qualifikation für Medizintechnik-Anwendungen
«Einen weiteren wichtigen Fortschritt erzielten wir mit der Qualifizierung unserer Mikro-Anlagentechnologie für Medizintechnik-Anwendungen in Übereinstimmung mit der ISO 13485», ergänzt W. Maurer.
Hierbei geht es nicht nur um die Anlage an sich. Darüber hinaus mussten Vorschriften und Prozeduren entwickelt werden, deren korrekte Anwendung im Rahmen der vom Betreiber vorzunehmenden Qualifizierung seiner Herstellprozesse die Zertifizierung gemäß ISO 13485 ermöglicht.
Dazu gehören beispielsweise nicht nur der Schneidprozess an sich, sondern auch die Reinigungsprozeduren zur Verhinderung einer Kontaminierung durch Verschleppung unerwünschter Substanzen.
Zur vollständigen Qualifizierung gehört abschließend auch der Nachweis der Prozessfähigkeit des Herstellverfahrens.
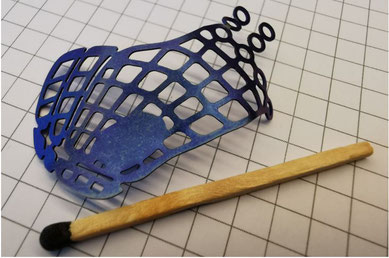
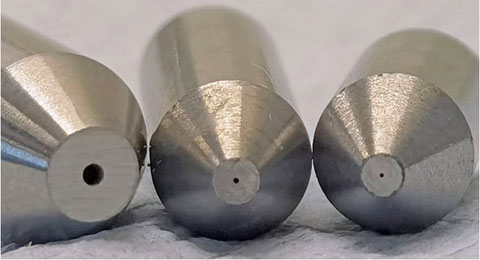
Höchstpräzision auch bei Blechen im Vollformat
Der bisher verfügbare Arbeitsbereich unserer F4-Maschinen auf 1.000x600mm bedingte sowohl technische als auch wirtschaftliche Begrenzungen», erläutert W. Maurer. Dies begann schon mit dem Zeitaufwand für das mehrfache Zerteilen der Blechplatten, die handelsüblich im Format 2.000x1.000mm geliefert werden.
Zudem verblieb danach ein 200mm breiter Reststreifen, der oft genug im Schrott landete. Mussten trotz der Größenbeschränkungen des Arbeitsbereichs Teile mit größeren Abmessungen hergestellt werden, so wurde ein Blech mit entsprechendem Übermaß eingespannt und nach einem ersten Bearbeitungsdurchgang um die erforderliche Distanz versetzt.
Beim Umspannen kommt es jedoch zwangsläufig zu Versatz- und Winkelfehlern und entsprechenden Qualitätseinbußen am Werkstück. Ebenfalls gravierend ist der Materialverlust durch den «Randeffekt» beim Verschachteln von Teilen auf der Arbeitsfläche sind.
In ungünstigen Fällen können diese Gitterverluste Werte von über 50% erreichen, was deutlich über dem üblichen Durchschnitt von 30% liegt.
Und last but not least kann eine größere Maschine je nach Jobcharakteristik wesentlich länger auch nach Schichtende oder ins Wochenende hinein mannlos laufen.
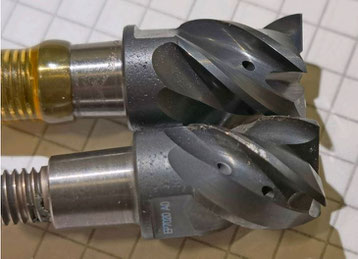
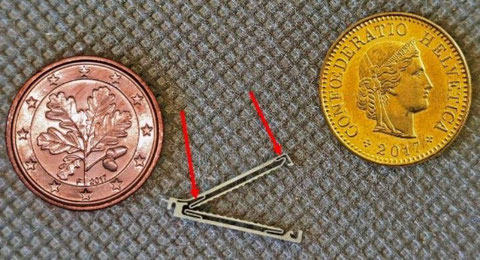
Kommentar schreiben